Compression Molding
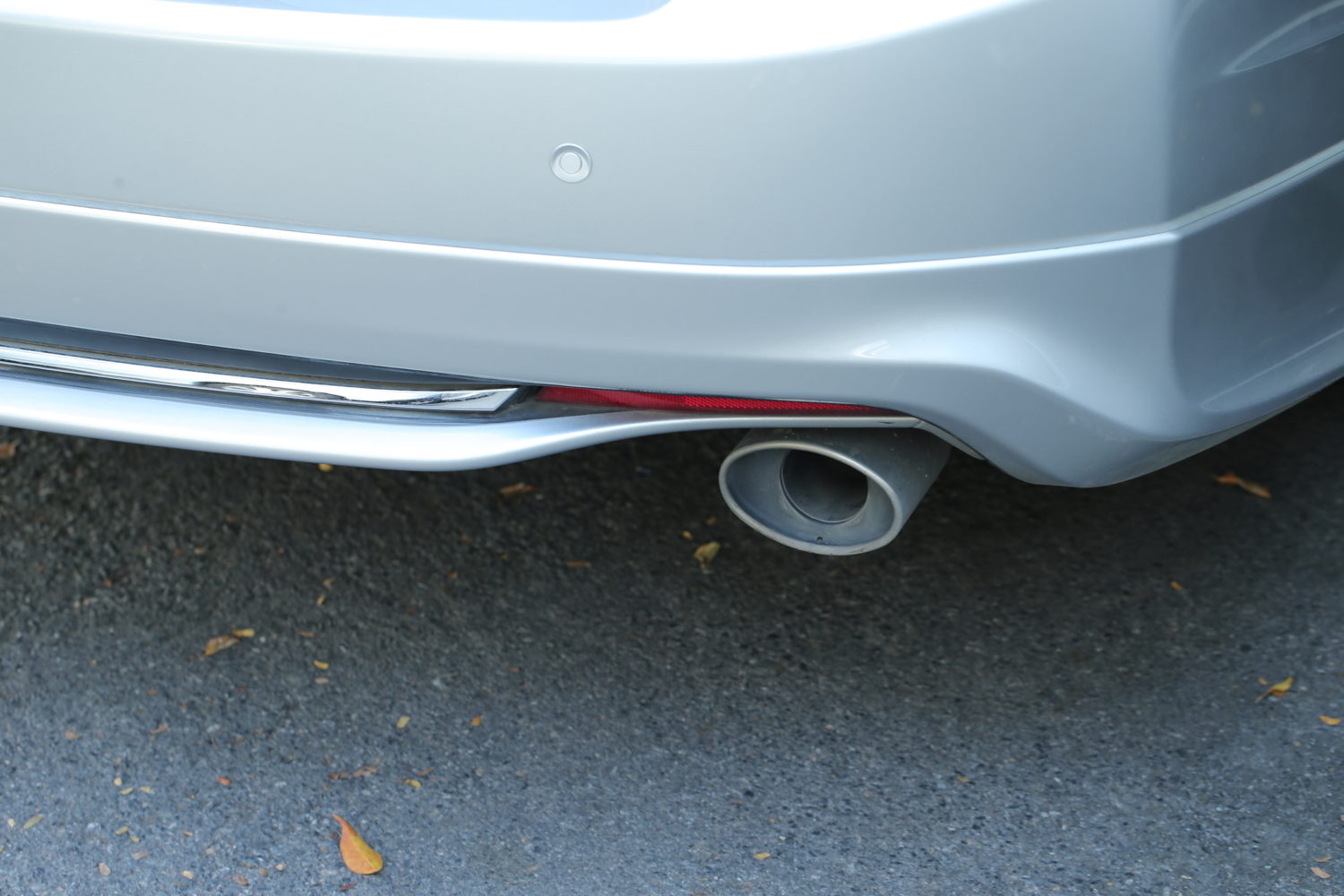
Compression molding uses heated steel tooling in high pressure presses to produce more complex, high volume parts with fast cycle times.
Compression molding is a high volume molding method that yields fast cycle times, high part uniformity, and allows for metal inserts, ribs and bosses to be molded in the part. There are several materials used in the compression molding processes including, sheet molding (SMC), bulk molding (BMC), thick molding (TMC), and wet molding (also known as liquid molding or cold molding). In the compression molding process, the heated matched metal mold set is mounted in a large hydraulic press. A pre-weighed charge of molding compound is loaded into the mold and the press is closed. Under the pressure and temperature of the tool set the material cures rapidly. Subsequent machining and finishing operations are minimal in compression molding so labor costs are reduced.
Sheet molding compound (SMC) is a thickened polyester/vinyl ester resin combined with chopped glass fibers and formed into a pliable sheet of material. SMC is made in a compounding process where fillers, thickening agents, release agents, pigments and chopped glass fibers are combined and configured into a sheet of a specified thickness. After being compounded, the SMC must “mature” for period of time to allow the thickening process to increase the viscosity. When ready, a pre-weighed charge of SMC is inserted in the tool cavity. The tool set is closed under the pressure of press, the SMC flows throughout the mold cavity, and cures under mold temperatures in the 3500 -4000 temperature range.
Bulk molding compound (BMC) is a highly viscous material created by mixing polyester or vinyl ester resin with chopped glass fibers, fillers, and other materials. BMC is inserted into the mold cavity as a “dough ball” rather than a sheet. Unlike sheet molding compounds (SMC), BMC requires no thickening time and can be used immediately after it is produced. BMC typically has a lower reinforcement content than SMC, permitting higher loadings of fillers to reduce costs. BMC is ideal for electrical applications as well as those requiring corrosion and heat resistance. It is often used for high volume production runs of parts for the automotive and transportation industries.
Compression molded parts are used in automotive, transportation, appliance and other high volume segments. Composites One provides all the materials that manufacturers need for compression molding, and a dedicated technical sales team who can help with any applications questions.