Reusable Bag Molding
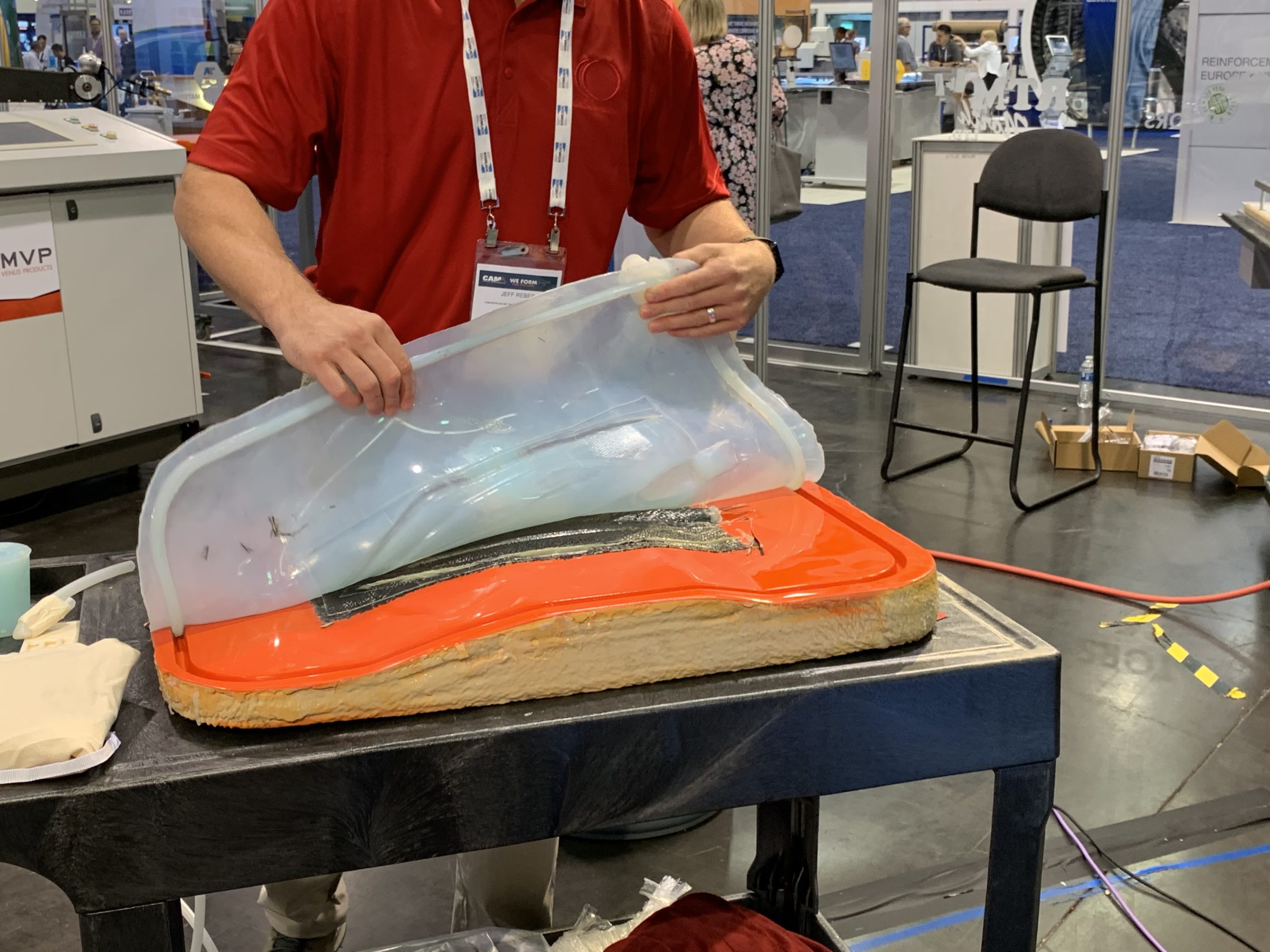
Reusable Bag Molding is similar to Vacuum Infusion Processing with the added advantage of a custom fit vacuum bag that is reusable up to hundreds of cycles. It eliminates disposable process materials such as vacuum bag film and sealant tape. It is much faster to seal the vacuum bag to the mold than in VIP. With excellent part-to-part consistency and ease of conversion from open molding, RSBM has become a viable alternative to open molding for numerous applications. Reusable Bag Molding incorporates a rigid “A” side or base mold and a flexible “B” side or counter mold that is made with silicone, latex or other rubber-like products. The bag may be made by brushing or spraying silicone material on the base mold and incorporating seals where the bag meets the mold flange. Like other closed mold processes, the base mold is loaded with dry fiber reinforcements, the flexible counter mold is put in place and a vacuum is drawn through ports incorporated into the bag. Catalyzed resin is introduced through the resin ports using a low pressure injection pump and the cavity is filled and cured. The advantages of Reusable Bag Molding include low tooling costs (existing open mold tooling can be easily converted), a reusable and repairable bag, significant reduction in HAP emissions, and ease in training operators with a relatively simple technology.
Reusable Bag Molding, also referred to as Closed Cavity Bag Molding or CCBM, is a simple, low-cost closed mold process that combines the benefits of Light RTM and Vacuum Infusion Process.
To see videos of Reusable Bag Molding visit the Closed Molding Knowledge Center.